Manual Data Collection
In the realm of manufacturing, data collection plays a pivotal role in ensuring smooth operations, optimizing processes, and making informed decisions. One of the primary methods employed for data collection is manual data collection. In this section, we will delve into the details of manual data collection, its benefits, and how it can be effectively implemented.
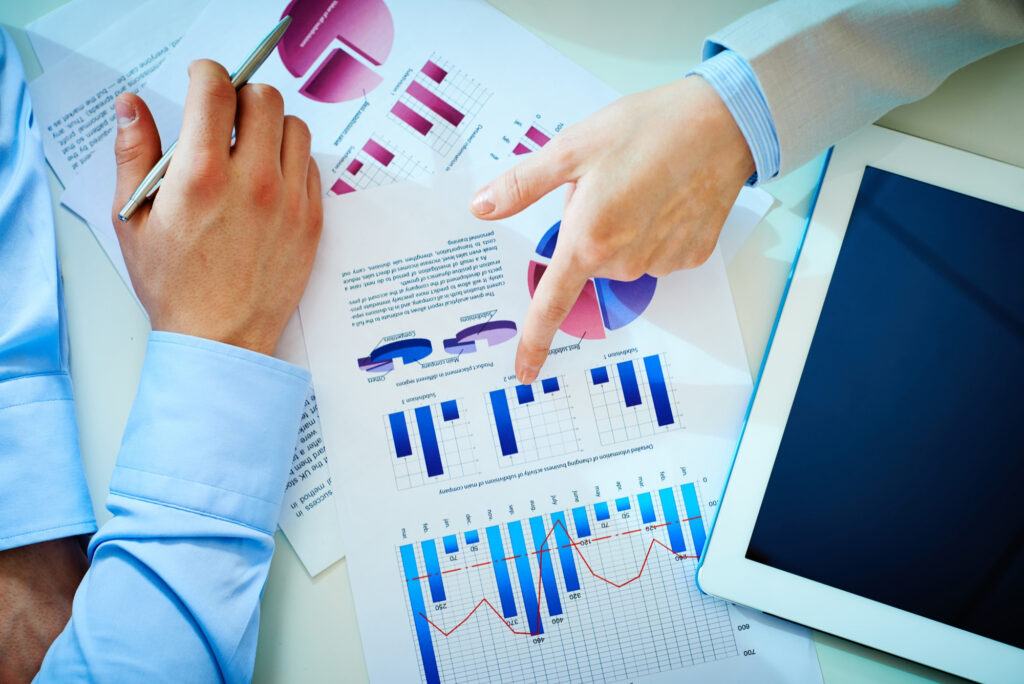
Benefits of Manual Data Collection
Manual data collection offers several advantages that make it a valuable approach in manufacturing environments. Firstly, it allows for real-time data acquisition, enabling manufacturers to gather information immediately as it is generated. This instantaneous data capture facilitates quick analysis and timely decision-making.
Moreover, manual data collection offers a higher degree of flexibility. It empowers operators and technicians to collect specific data points tailored to their unique requirements, allowing for a more comprehensive understanding of the manufacturing processes. Additionally, manual data collection can be easily modified or adapted to accommodate evolving needs or changing parameters, ensuring that the collected data remains relevant and actionable.
Implementing Manual Data Collection
To effectively implement manual data collection, manufacturers should establish clear protocols and guidelines. This includes defining the specific data points to be collected, outlining the frequency and timing of data collection, and training operators on the data collection procedures.
It is crucial to ensure accuracy in manual data collection. Manufacturers should employ standardized data entry methods, such as using digital forms or templates, to minimize human error. Regular quality checks and audits should also be conducted to validate the collected data and identify any inconsistencies or discrepancies.
In addition, manual data collection can be enhanced through the use of supporting tools and technologies. For instance, barcode scanners or handheld devices can be employed to streamline the process and minimize the time required for data entry. Integrating these tools with centralized data management systems further enhances data organization and accessibility.
Automated Data Collection
While manual data collection is widely used and effective, the advent of technology has introduced automated data collection methods that offer increased efficiency, accuracy, and scalability. Automated data collection leverages various technological solutions to capture and process data seamlessly, eliminating the need for manual intervention.
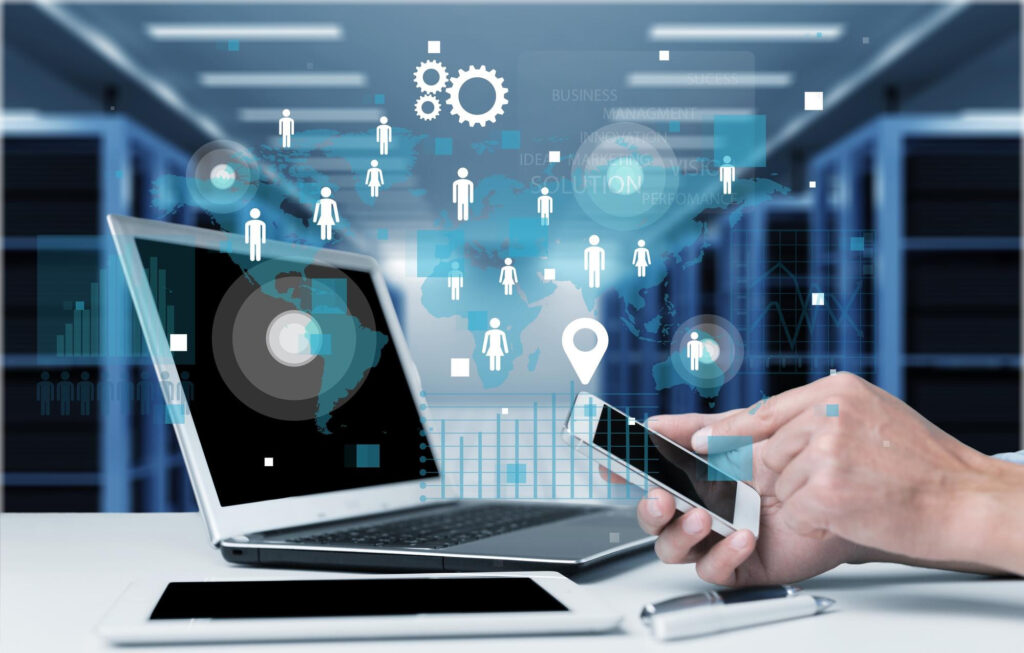
Benefits of Automated Data Collection
Automated data collection offers numerous advantages over manual methods. First and foremost, it significantly reduces the risk of human error, ensuring data accuracy and reliability. By automating the data collection process, manufacturers can eliminate the potential for manual data entry mistakes, transcription errors, or data omission.
Furthermore, automated data collection enables real-time data acquisition and analysis. Data is captured automatically as it is generated, providing immediate insights into the manufacturing operations. This enables timely decision-making, rapid troubleshooting, and the ability to identify and rectify issues promptly, thereby minimizing downtime and maximizing productivity.
Additionally, automated data collection improves data consistency and standardization. By employing predefined data collection protocols, manufacturers can ensure that data is collected uniformly across different processes, shifts, or facilities. This enhances data comparability and enables comprehensive analysis and benchmarking.
Implementing Automated Data Collection
To implement automated data collection effectively, manufacturers need to invest in suitable technologies and infrastructure. This may include deploying sensors, Internet of Things (IoT) devices, or machine interfaces that capture data directly from equipment or machinery. The collected data can then be transmitted wirelessly to a centralized database or cloud storage for further processing and analysis.
It is essential to integrate the automated data collection system with data analytics and visualization tools. These tools enable manufacturers to derive actionable insights from the collected data, visualize performance trends, and generate real-time reports or dashboards for informed decision-making.
Manufacturers should also consider the cybersecurity aspects of automated data collection. With the increasing connectivity and digitalization of manufacturing processes, it is crucial to implement robust cybersecurity measures to protect sensitive data from unauthorized access or potential cyber threats.
Manufacturing Metrics to Measure
In manufacturing, metrics play a vital role in assessing performance, identifying areas for improvement, and driving operational excellence. Accurate and reliable data collection is instrumental in measuring these metrics effectively. Here are some key manufacturing metrics commonly measured:
1. Overall Equipment Effectiveness (OEE)
OEE is a comprehensive metric that assesses the performance of equipment or machinery by considering three factors: availability, performance efficiency, and quality rate. It provides insights into the overall equipment utilization, highlighting opportunities for enhancing productivity and reducing downtime.
2. Cycle Time
Cycle time measures the time required to complete a specific manufacturing process or operation. By monitoring cycle time, manufacturers can identify bottlenecks, optimize workflow, and improve overall efficiency.
3. Defect Rate
Defect rate quantifies the number of defective units or products produced during a manufacturing process. It helps identify quality issues, evaluate the effectiveness of quality control measures, and drive continuous improvement initiatives.
4. Throughput
Throughput measures the rate at which units or products are produced within a given time frame. It enables manufacturers to evaluate production capacity, optimize resource allocation, and identify opportunities for increasing output.
5. Scrap and Rework Costs
Scrap and rework costs measure the financial impact of defective or non-compliant units. By tracking these costs, manufacturers can identify the root causes of defects, implement corrective actions, and reduce waste.
In conclusion, data collection methods in manufacturing encompass both manual and automated approaches, each offering unique benefits and advantages. Manufacturers should carefully evaluate their specific requirements and operational context to determine the most suitable data collection strategy. By leveraging accurate and comprehensive data, manufacturing organizations can optimize their processes, drive continuous improvement, and achieve operational excellence in today’s dynamic business landscape.