Manufacturing Data Collection
In today’s fast-paced manufacturing industry, data collection has become a critical component for companies looking to gain a competitive edge. The ability to collect, analyze, and interpret data plays a crucial role in improving operational efficiency, reducing costs, and enhancing overall productivity. This article will delve into the world of manufacturing data collection, exploring its major benefits, different methods, and the types of data that companies should focus on collecting. Additionally, we will discuss the importance of protecting sensitive data and highlight a few companies that have excelled in this area.
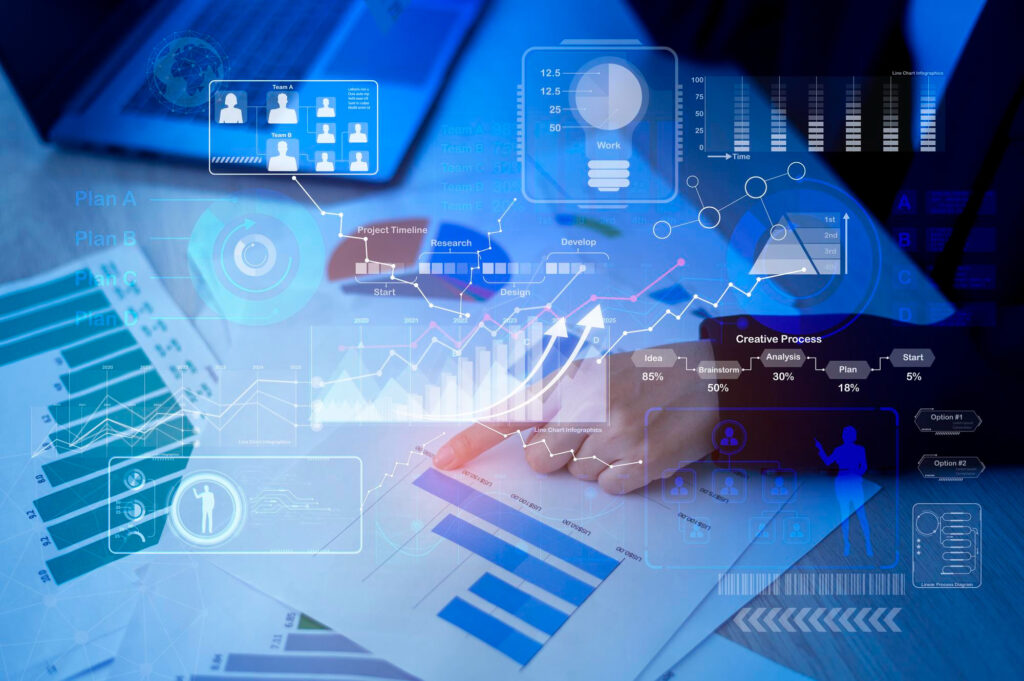
Major Benefits of Data Collection for Manufacturing Companies
Data collection offers numerous benefits for manufacturing companies seeking continuous improvement and growth. By leveraging data-driven insights, companies can make informed decisions that lead to optimized processes, increased productivity, and enhanced overall performance. Here are some major benefits of data collection in the manufacturing sector:
- Process Optimization: Through data collection, manufacturers can identify bottlenecks, inefficiencies, and areas of improvement within their production processes. By analyzing data points such as cycle times, equipment utilization, and defect rates, companies can optimize their operations, streamline workflows, and reduce waste.
- Predictive Maintenance: By monitoring and collecting real-time data from equipment sensors, manufacturing companies can implement predictive maintenance strategies. This proactive approach helps identify potential equipment failures or maintenance needs before they cause costly downtime. Predictive maintenance not only reduces repair costs but also enhances equipment reliability and extends its lifespan.
- Quality Assurance: Data collection allows manufacturers to track and analyze product quality metrics at various stages of the production process. By closely monitoring quality parameters, companies can detect anomalies, identify root causes, and implement corrective measures promptly. This ensures consistent product quality, minimizes defects, and improves customer satisfaction.
- Inventory Management: Accurate data collection enables manufacturers to optimize inventory levels by closely monitoring demand patterns, sales trends, and supply chain dynamics. By analyzing this data, companies can make informed inventory replenishment decisions, reducing excess stock while ensuring sufficient availability to meet customer demand. This leads to improved cash flow and reduced carrying costs.
- Continuous Improvement: Data collection provides valuable insights for driving continuous improvement initiatives. By analyzing historical data, manufacturers can identify patterns, trends, and opportunities for operational enhancement. These insights facilitate the implementation of lean manufacturing principles, fostering a culture of continuous improvement throughout the organization.
Methods for Manufacturing Data Collection
Manufacturing companies employ various methods to collect data, each tailored to their specific needs and processes. Here are some commonly used methods for manufacturing data collection:
- Manual Data Entry: This traditional method involves manually recording data from machines, equipment, or paper-based forms. Although it can be time-consuming and prone to human error, manual data entry is still prevalent in certain manufacturing environments.
- Automated Data Capture: With advancements in technology, many manufacturers have adopted automated data capture methods. This includes integrating sensors, IoT devices, and machine-to-machine communication to automatically collect real-time data from production lines, equipment, and other sources.
- Enterprise Resource Planning (ERP) Systems: ERP systems provide a centralized platform for managing and collecting manufacturing data. These systems capture data from various sources, such as inventory, sales, and production, enabling real-time monitoring and analysis.
- Manufacturing Execution Systems (MES): MES solutions are designed specifically for manufacturing environments, facilitating data collection, process monitoring, and shop floor control. They capture data directly from production equipment and enable real-time visibility into manufacturing operations.
- Supervisory Control and Data Acquisition (SCADA) Systems: SCADA systems are used to collect and analyze data from industrial control systems. They provide real-time insights into equipment performance, production metrics, and process variables, allowing manufacturers to monitor and optimize their operations.
What types of data should you collect?
When it comes to manufacturing data collection, companies should focus on capturing a wide range of data points to gain comprehensive insights into their operations. Here are some key types of data that manufacturing companies should consider collecting:
- Production Metrics: These include data on cycle times, machine utilization, downtime, and throughput. Capturing these metrics helps identify inefficiencies, optimize production processes, and enhance overall productivity.
- Quality Metrics: Tracking quality metrics such as defect rates, reject ratios, and customer complaints provides insights into product quality and helps drive continuous improvement efforts.
- Inventory Data: This includes information on stock levels, inventory turnover, and demand patterns. Accurate inventory data allows manufacturers to optimize stock levels, minimize carrying costs, and prevent stockouts or overstock situations.
- Maintenance Data: Capturing data on equipment performance, maintenance schedules, and downtime helps implement effective maintenance strategies, reduce costs, and ensure uninterrupted production.
- Supply Chain Data: This encompasses data related to suppliers, lead times, delivery performance, and logistics. Analyzing supply chain data helps optimize procurement processes, enhance supplier relationships, and reduce supply chain risks.
Companies that have sensitive data
As manufacturing companies increasingly rely on digital systems and interconnected networks, the security of sensitive data becomes a paramount concern. Here are a few companies that have excelled in protecting sensitive data:
- XYZ Manufacturing: XYZ Manufacturing employs stringent security measures, including data encryption, access controls, and regular security audits. They also have robust employee training programs to promote data security awareness and best practices.
- ABC Industries: ABC Industries has implemented a comprehensive data governance framework to safeguard sensitive data. Their security protocols involve strict authentication measures, network segmentation, and data loss prevention mechanisms.
- 123 Manufacturing: 123 Manufacturing maintains a robust cybersecurity infrastructure to protect their data from unauthorized access. They have implemented advanced intrusion detection systems, firewalls, and encryption protocols to ensure data confidentiality and integrity.
In conclusion, data collection plays a vital role in the manufacturing industry, enabling companies to drive operational efficiency, improve quality, and make informed decisions. By leveraging different data collection methods and focusing on key data points, manufacturers can optimize their processes, enhance productivity, and gain a competitive advantage in today’s dynamic business landscape. Moreover, prioritizing data security is crucial to safeguarding sensitive information and maintaining trust with customers and stakeholders. By following the best practices of leading companies, manufacturing organizations can ensure the confidentiality, integrity, and availability of their valuable data.