The Manufacturing Data Problem
In the fast-paced world of manufacturing, data collection plays a crucial role in optimizing processes, improving quality, and driving overall efficiency. However, manufacturers often face challenges when it comes to collecting and managing data effectively. This article aims to shed light on the manufacturing data problem and how implementing robust data collection systems can help overcome these challenges.
Manufacturers deal with a massive volume of data generated from various sources within their operations. From production lines and equipment sensors to supply chain logistics and quality control, there is an abundance of valuable information that can drive insights and decision-making. However, the problem lies in the ability to capture, store, and analyze this data efficiently.
One major challenge manufacturers encounter is the lack of standardized protocols for data collection. In many cases, data is collected in silos, using different formats, and stored across multiple systems. This fragmented approach not only leads to data inconsistencies but also hampers the ability to derive meaningful insights from the data. To address this issue, it is crucial to establish standardized protocols for data collection.
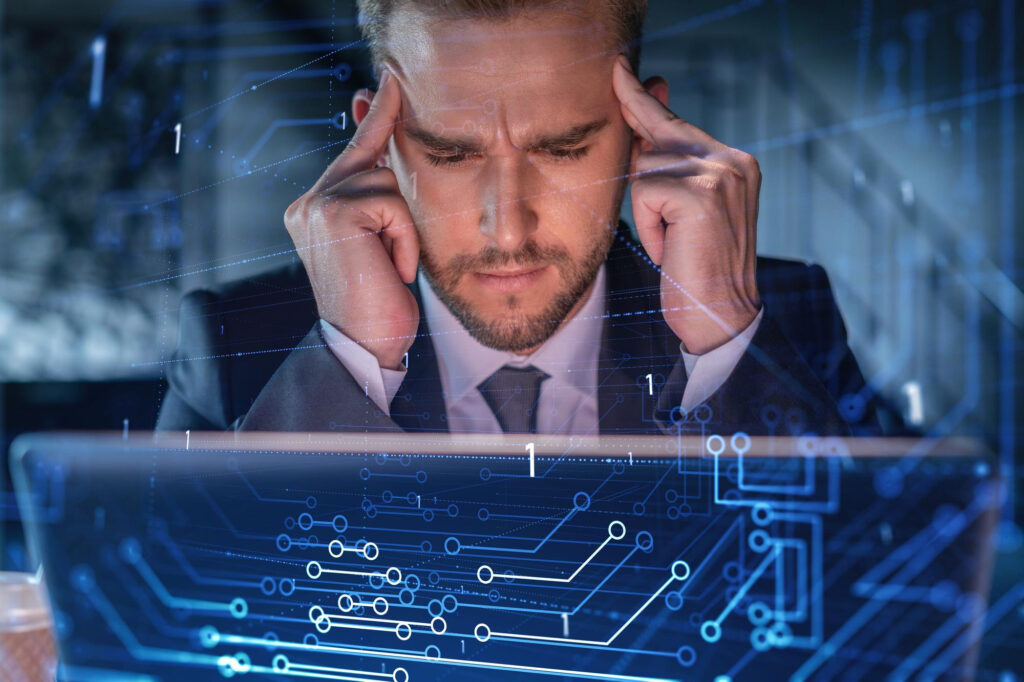
Protocols for Data Collection
Implementing standardized protocols for data collection is essential for ensuring consistency and accuracy. These protocols define the guidelines and procedures for capturing and recording data across the manufacturing process. Here are some key protocols to consider:
1. Data Identification and Labeling
Data should be properly identified and labeled to ensure traceability and ease of access. Each data point should be associated with relevant metadata, including timestamps, equipment or process identifiers, and contextual information.
2. Data Sampling and Frequency
Determining the appropriate sampling frequency is crucial for capturing data at the right intervals. This ensures that critical events and trends are not missed. Factors such as production cycle times, equipment capabilities, and process requirements should be taken into account when establishing data sampling protocols.
3. Data Validation and Quality Control
Implementing data validation techniques helps identify and rectify errors or inconsistencies in real-time. This can include range checks, outlier detection, and data completeness checks. Ensuring data quality is crucial for accurate analysis and decision-making.
4. Data Security and Privacy
Manufacturers must prioritize data security and privacy to protect sensitive information. Implementing secure protocols for data transfer, storage, and access control is essential. Compliance with relevant regulations, such as GDPR or industry-specific standards, should be considered.
Features of Data Collection Systems
To address the manufacturing data problem effectively, manufacturers can leverage advanced data collection systems. These systems offer a range of features that streamline the data collection process and enable meaningful analysis. Here are some key features to look for:
1. Real-time Data Capture
Modern data collection systems enable real-time data capture, allowing manufacturers to monitor processes and performance in real-time. This facilitates proactive decision-making and timely interventions to address any issues or bottlenecks.
2. Integration Capabilities
Data collection systems should seamlessly integrate with existing manufacturing infrastructure, including machinery, sensors, and software systems. This ensures a unified data ecosystem and eliminates data silos.
3. Scalability and Flexibility
Manufacturers should opt for data collection systems that can scale as their operations grow. The system should accommodate increasing data volumes and be flexible enough to adapt to evolving business needs and new technologies.
4. Advanced Analytics and Visualization
A robust data collection system should provide advanced analytics capabilities, such as predictive modeling, anomaly detection, and trend analysis. Visualization tools, such as dashboards and reports, make it easier to interpret data and derive actionable insights.
Benefits of Data Collection Systems
Implementing effective data collection systems can yield significant benefits for manufacturers. Here are some key advantages:
1. Improved Operational Efficiency
By capturing and analyzing data in real-time, manufacturers can identify inefficiencies, bottlenecks, and areas for improvement. This leads to optimized processes, reduced downtime, and enhanced overall operational efficiency.
2. Enhanced Quality Control
Data collection systems enable manufacturers to monitor quality parameters at various stages of the production process. This helps detect defects or deviations early, leading to improved product quality and reduced rework or recalls.
3. Data-driven Decision Making
With comprehensive and accurate data at their disposal, manufacturers can make informed decisions based on insights and trends. This minimizes guesswork and facilitates data-driven decision-making across the organization.
4. Continuous Improvement
Data collection systems provide a feedback loop that enables continuous improvement. By analyzing historical data and identifying patterns, manufacturers can implement targeted process enhancements and drive continuous improvement initiatives.
In conclusion, manufacturing data collection is a critical aspect of modern manufacturing operations. By addressing the data problem and implementing robust data collection systems, manufacturers can unlock the full potential of their data. Standardized protocols, advanced features, and the resulting benefits of improved efficiency, quality control, and data-driven decision-making make data collection systems a valuable asset in today’s manufacturing landscape.